Welding WPS Explained: Key Elements and Conveniences for Your Welding Procedures
Welding WPS Explained: Key Elements and Conveniences for Your Welding Procedures
Blog Article
Getting Welding Quality: Introducing the Keys of WPS Implementation and Optimization
In the world of welding, attaining quality is a quest that hinges on the thorough application and optimization of Welding Treatment Requirements (WPS) By delving right into the crucial components, strategies, challenges, and finest methods linked with WPS, a globe of welding quality waits for those who are willing to explore its midsts.
Significance of WPS in Welding
The Importance of Welding Procedure Specifications (WPS) in the welding industry can not be overstated, acting as the backbone for guaranteeing consistency, high quality, and security in welding operations. A WPS offers in-depth guidelines on just how welding is to be accomplished, consisting of crucial variables such as materials, welding processes, joint design, filler steels, preheat and interpass temperatures, welding currents, voltages, travel rates, and more. By adhering to a distinct WPS, welders can preserve uniformity in their work, causing consistent weld top quality throughout different projects.
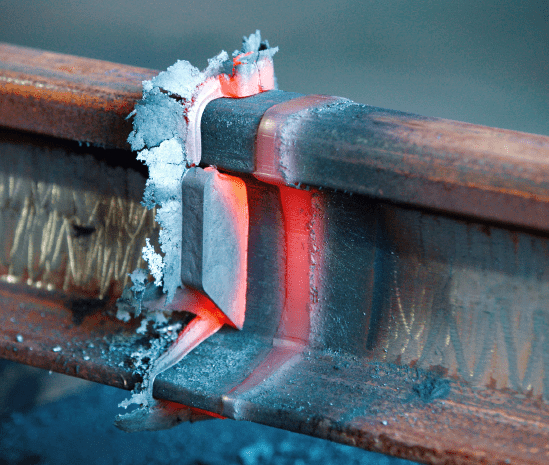
Secret Components of WPS
Reviewing the important components of a welding procedure requirements (WPS) is important for recognizing its duty in welding procedures. A comprehensive WPS includes numerous crucial elements that lead welders in attaining high quality and consistency in their job. One critical element of a WPS is the welding procedure requirements, which describes the details welding procedures to be utilized, such as gas tungsten arc welding (GTAW) or secured steel arc welding (SMAW) Furthermore, the WPS consists of information on the welding products, such as the kind and specifications of the base metal and filler metal to be made use of. The WPS also specifies important variables like welding specifications, interpass and preheat temperature level needs, and post-weld warm treatment procedures. Additionally, it includes info on joint style, fit-up, and any kind of unique strategies or precautions needed for the welding procedure. By integrating these crucial elements into the WPS, welding procedures can be standardized, ensuring high quality, effectiveness, and safety and security in welding procedures.
Strategies for WPS Optimization
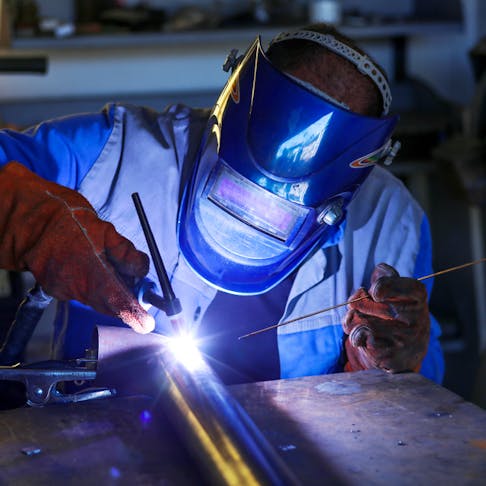
Secondly, training and certification of welding employees according to the specific demands of the WPS is Going Here vital. Offering thorough training programs and ensuring that welders are accredited to execute procedures detailed in the WPS can cause better welds and minimized rework.
In addition, leveraging modern technology such as welding software and monitoring systems can aid in enhancing WPS. These tools can help in monitoring variables, making certain parameters are within specified limits, and providing real-time feedback to welders, enabling them to make prompt modifications for enhanced weld quality.
Typical Obstacles and Solutions
Encountering barriers in carrying out the methods for WPS optimization can prevent welding operations' efficiency and quality. One usual difficulty is insufficient training or understanding of the welding procedure requirements (WPS) amongst the welding group.
One more challenge is the absence of correct paperwork and record-keeping, which is important for WPS optimization. Without clear records of welding criteria, materials utilized, and inspection outcomes, it ends up being tough to determine areas for renovation and ensure consistency in welding processes. Carrying out a robust documents system, such as digital welding monitoring software application, can help enhance record-keeping and assist in data evaluation for continuous enhancement.
Additionally, irregular welding equipment calibration and upkeep can posture a substantial challenge to WPS optimization. Normal equipment checks, calibration, and upkeep timetables ought to be complied with strictly to make sure that welding specifications are properly controlled and preserved within the defined tolerances (welding WPS). By attending to these usual obstacles with proactive options, welding operations can improve performance, high quality, and total welding quality
Finest Practices for WPS Application
To ensure successful WPS execution in welding procedures, adherence to market criteria and thorough attention to detail are extremely important. When launching WPS implementation, it is important to begin by thoroughly recognizing the specific welding demands of the job. This requires a comprehensive evaluation of the welding procedure specs, products to be bonded, and the environmental conditions in which the welding will take location.
As soon as the needs are clear, the next step is to choose the proper welding treatment that aligns with these specifications. This involves seeking advice from the relevant codes and standards, such as those supplied by the American Welding Culture (AWS) or the International Organization for Standardization (ISO), to ensure compliance and quality.
Moreover, documenting the entire WPS execution process is important for traceability and quality assurance. In-depth documents must be maintained regarding welding criteria, product prep work, interpass and preheat temperatures, welding consumables used, and any deviations from the initial treatment. Normal audits and testimonials of the WPS can assist determine areas for improvement and make certain recurring optimization of the welding process.
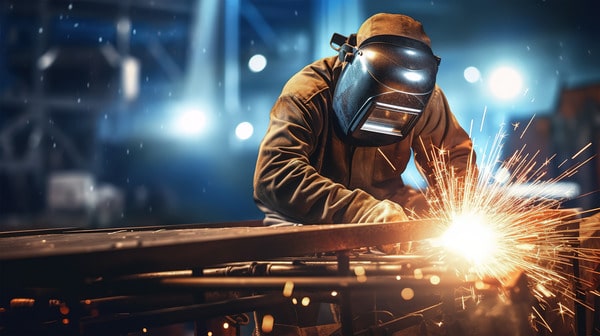

Verdict
Finally, the application and optimization of Welding Treatment Specifications (WPS) is Resources vital for achieving welding quality. By recognizing the crucial elements of WPS, executing reliable strategies for optimization, resolving common difficulties, and following finest techniques, welders can guarantee high-grade welds and safe working problems. It is important for specialists in the welding industry to prioritize the proper execution of WPS to improve overall welding efficiency and attain desired results.
The Relevance of Welding Full Report Procedure Specs (WPS) in the welding market can not be overstated, serving as the foundation for making certain consistency, high quality, and safety and security in welding procedures. A WPS provides comprehensive directions on how welding is to be brought out, consisting of necessary variables such as products, welding processes, joint style, filler steels, interpass and preheat temperature levels, welding currents, voltages, travel speeds, and much more. One important element of a WPS is the welding process requirements, which details the specific welding procedures to be used, such as gas tungsten arc welding (GTAW) or shielded steel arc welding (SMAW) By incorporating these crucial components right into the WPS, welding treatments can be standard, ensuring quality, efficiency, and safety in welding procedures.
It is vital for professionals in the welding industry to prioritize the appropriate execution of WPS to boost total welding efficiency and accomplish preferred results.
Report this page